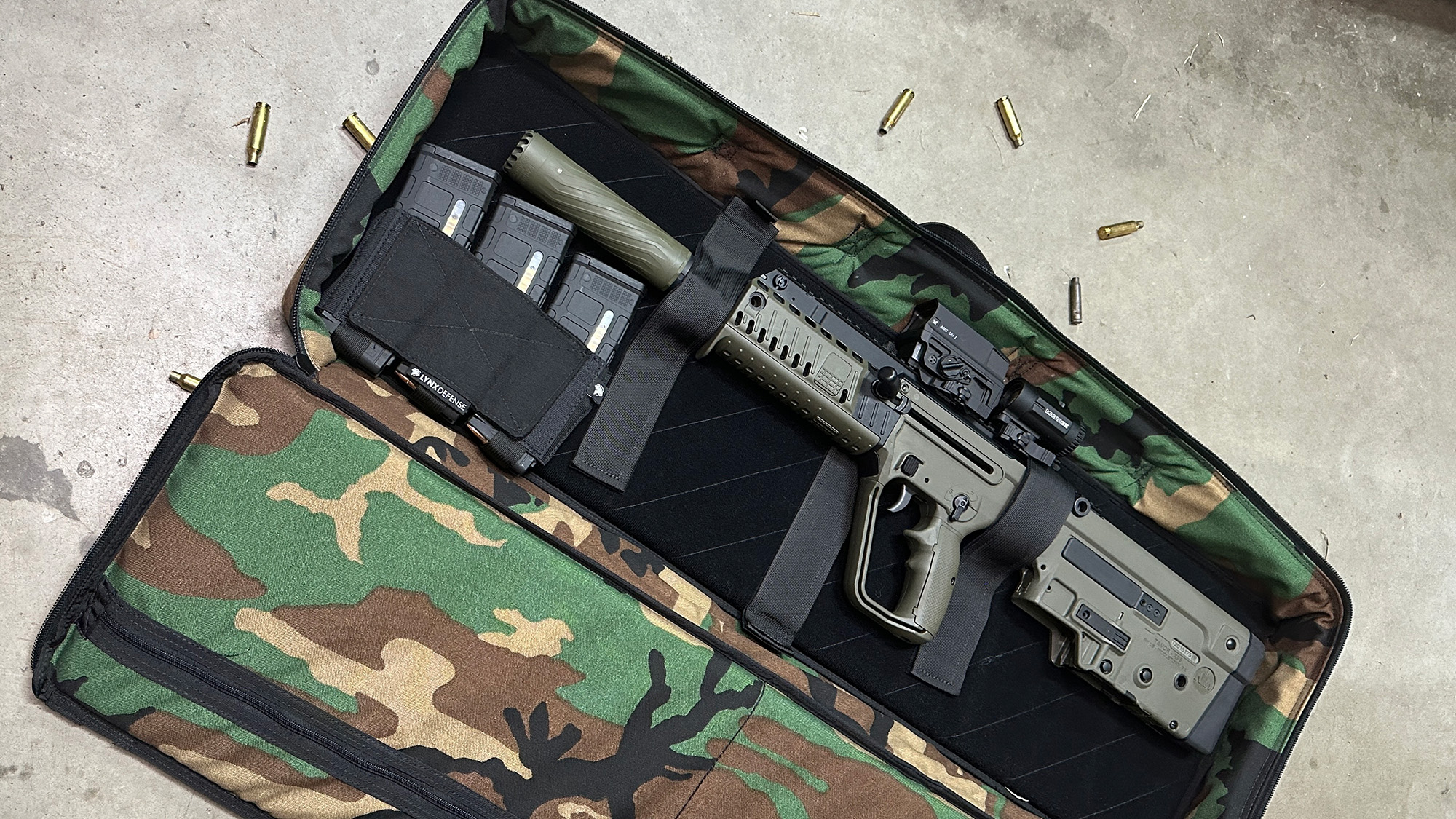
Ready to see what we have coming?
Lynx Defense will release some new things soon. Let us deliver them right to your inbox!
Lynx Defense will release some new things soon. Let us deliver them right to your inbox!
Lynx Defense
103 N Raiford St
Selma, NC 27576